The oil and gas industry is known for its complex infrastructure, demanding working environments, and the necessity of precision and reliability. From the extraction of raw materials to refining processes, companies in this sector rely on robust technologies to ensure smooth, efficient, and safe operations. Over the last few decades, one technological advancement that has had a profound impact on the oil and gas sector is laser cutting. This revolutionary tool has transformed the way metal components are fabricated, leading to greater accuracy, improved safety, and enhanced cost efficiency.
Houston, Texas, often regarded as the energy capital of the world, is at the forefront of this transformation. Companies like Rapid Turn Laser & Machine, LLC are helping drive innovation in the oil and gas industry by providing cutting-edge laser cutting and metal fabrication services. This article explores how laser cutting technology has reshaped the oil and gas landscape, offering significant benefits across various facets of the industry.
The Demands of the Oil & Gas Industry
To understand the full impact of laser cutting on the oil and gas industry, it is important to first recognize the unique demands and challenges of this sector. The industry requires equipment that can withstand extreme conditions, from high pressures deep underground to extreme temperatures during refining processes. Additionally, components used in oil rigs, pipelines, and refineries must be highly precise to prevent costly breakdowns or safety hazards.
For decades, traditional methods like plasma cutting, water jet cutting, and manual machining were widely used to fabricate metal components for the oil and gas sector. While effective, these methods often required substantial time, labor, and material waste. Moreover, the margins for error were relatively high, leading to inefficiencies in production and sometimes causing delays in projects.
As the industry has evolved, so too have the technologies used to meet its needs. Laser cutting has quickly become the preferred choice for fabricating metal parts used in oil rigs, pipelines, subsea systems, and refineries due to its unparalleled precision, speed, and efficiency.
The Rise of Laser Cutting in Oil & Gas
Laser cutting is a method that uses a high-powered laser beam to cut through various materials, typically metals such as steel, aluminum, or titanium, with extraordinary precision. The process is computer-controlled, allowing for detailed designs and extremely tight tolerances to be achieved. In an industry like oil and gas, where accuracy and reliability are critical, this level of precision is invaluable.
One of the most significant advantages of laser cutting technology in this sector is the ability to create intricate and custom parts that are tailored to the specific needs of an oil or gas project. These projects often involve complex systems of pipelines, valves, and machinery that need to fit together perfectly. A misaligned component, or one with even the slightest flaw, could lead to dangerous leaks or other catastrophic failures. With laser cutting, manufacturers can meet stringent quality requirements, ensuring that each part performs its function flawlessly.
Additionally, laser cutting reduces the amount of material waste compared to other cutting methods. For a company in the oil and gas industry, this leads to significant cost savings, as materials like high-grade steel and titanium are expensive. Less waste translates to lower material costs, which is a huge benefit for businesses working on tight budgets and timeframes.
Improved Efficiency in Pipeline Construction
One of the most notable applications of laser cutting in the oil and gas industry is in the construction and maintenance of pipelines. The global network of oil and gas pipelines spans over 2.7 million kilometers, making it a crucial aspect of energy infrastructure. Pipeline construction requires precise fabrication of thousands of components, including pipes, valves, and flanges.
In the past, traditional cutting methods were often used to shape these parts, which could result in imperfect edges and inconsistent measurements. With laser cutting, manufacturers can produce parts that are perfectly uniform, down to the millimeter. This not only ensures a better fit but also helps to reduce the risk of pipeline leaks, which are a significant concern for the industry.
Pipeline leaks can be incredibly costly. According to a report by the U.S. Department of Transportation, pipeline spills in the U.S. have caused over $8 billion in damages over the last two decades. Many of these incidents were the result of poorly constructed or worn-out components. By using laser cutting to create precise parts, companies can drastically reduce the likelihood of such events, improving both safety and operational efficiency.
Moreover, laser cutting speeds up the construction process. Traditional methods like manual machining can be time-consuming, especially when working with large quantities of parts. Laser cutting, on the other hand, can cut through metal quickly and with high accuracy, reducing the time required to fabricate critical pipeline components. This translates to faster project completion, which is especially beneficial in an industry where downtime can result in substantial financial losses.
Enhanced Safety and Reliability
Safety is a top priority in the oil and gas industry. Workers are often exposed to hazardous environments, whether on offshore drilling platforms, in refineries, or along vast pipelines. The materials and equipment used in these settings must be highly reliable to avoid accidents and malfunctions. Laser cutting technology offers several safety advantages that help ensure the reliability of critical components.
First, laser-cut parts are less prone to imperfections such as burrs or rough edges, which are common with traditional cutting methods like plasma or water jet cutting. These imperfections can weaken a component over time or cause issues during assembly. A clean, smooth cut from a laser reduces the risk of failure, ensuring that parts will hold up under extreme conditions.
Second, the ability to create highly intricate designs with laser cutting allows for the production of custom components that fit precisely into existing systems. This eliminates the need for on-site adjustments, which can introduce errors and lead to dangerous situations. In the oil and gas industry, even minor deviations in the specifications of a part can lead to equipment malfunctions, leaks, or explosions. The precision offered by laser cutting minimizes these risks.
Furthermore, laser cutting systems are automated, reducing the need for manual labor during the fabrication process. This not only speeds up production but also reduces the risk of human error, which can be a significant factor in accidents. By automating the cutting process, companies can ensure that each part is made to exact specifications, improving the overall safety and reliability of their operations.
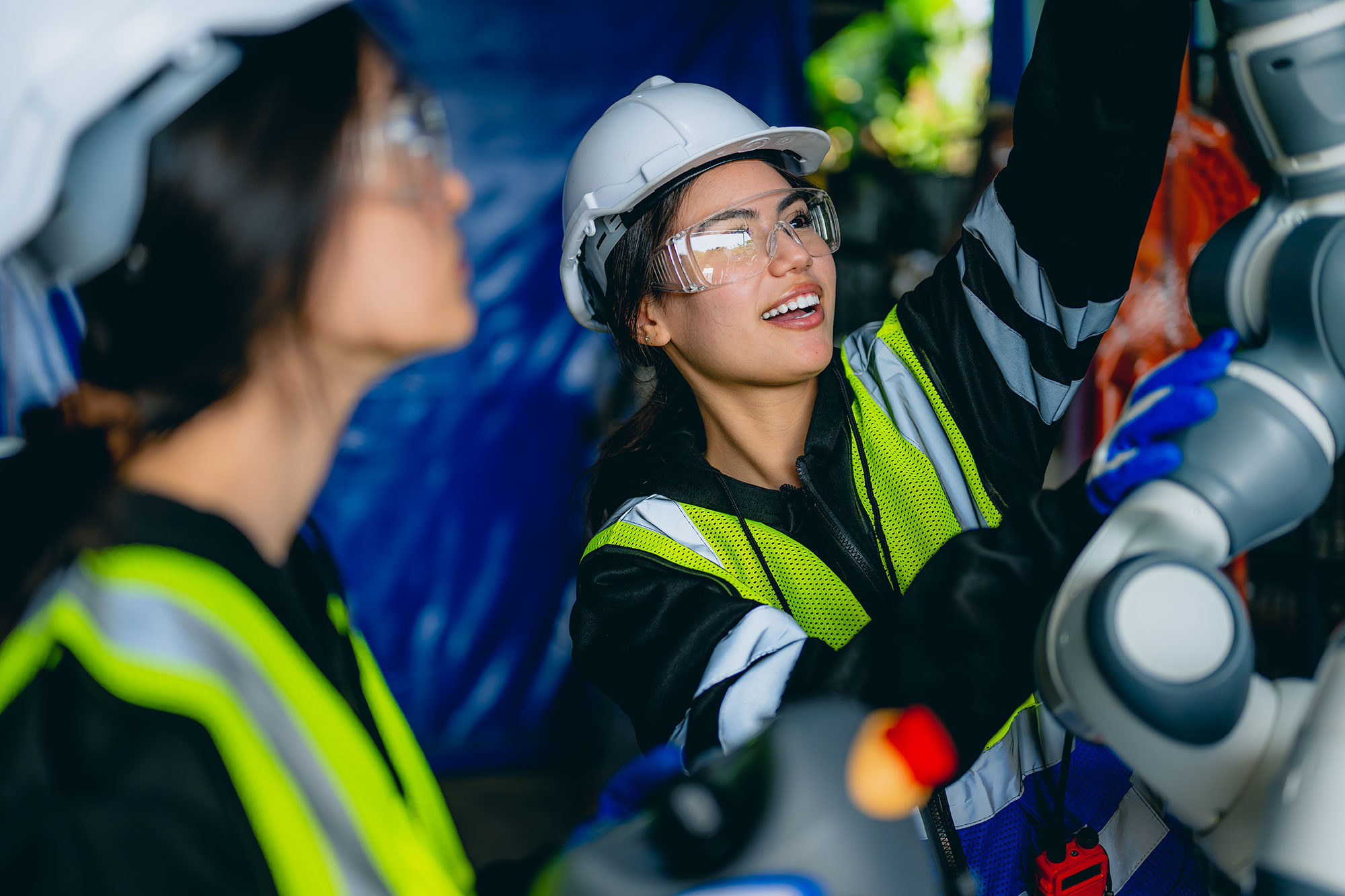
Supporting Subsea and Offshore Applications
In addition to pipelines and refineries, laser cutting technology is also making a significant impact in subsea and offshore applications. These environments present unique challenges due to the high pressures, corrosive conditions, and logistical difficulties involved in transporting equipment to and from offshore platforms.
Subsea components, such as those used in underwater pipelines and drilling systems, require an exceptional level of precision and durability. Laser cutting is particularly well-suited for fabricating these components because it allows manufacturers to create complex geometries with exact tolerances. For example, subsea flanges and connectors must be able to withstand immense pressures, and any deviation from the design could result in catastrophic failure. Laser cutting ensures that these parts are fabricated to the highest standards, reducing the risk of malfunction.
Moreover, offshore platforms rely on large quantities of fabricated metal components, such as structural supports, handrails, and safety barriers. These parts must be corrosion-resistant to withstand the harsh marine environment. Laser cutting is an ideal method for cutting stainless steel and other corrosion-resistant materials, ensuring that offshore platforms remain safe and operational for extended periods.
Cost Efficiency and Competitive Advantage
The oil and gas industry is highly competitive, and companies are always looking for ways to reduce costs without compromising on quality. Laser cutting provides a competitive advantage by offering cost efficiencies in several areas.
First, the automation of laser cutting reduces the need for manual labor, which can be costly and prone to errors. Fewer workers are needed to oversee the cutting process, allowing companies to allocate their workforce to other important tasks.
Second, as mentioned earlier, laser cutting produces less waste than traditional methods. This not only reduces the cost of materials but also minimizes the environmental impact of operations—something that is becoming increasingly important in an industry under pressure to reduce its carbon footprint.
In addition, laser cutting offers greater flexibility when it comes to customization. Oil and gas projects often require parts that are tailored to specific requirements, whether they involve unusual shapes, sizes, or materials. Laser cutting can easily accommodate these needs, allowing companies to offer bespoke solutions to their clients without incurring significant additional costs.
Finally, laser cutting leads to faster project completion times. In an industry where time is money, being able to deliver projects on or ahead of schedule can be a major selling point for a company. By speeding up the fabrication process, laser cutting helps companies complete projects more quickly, reducing downtime and improving overall profitability.
The Future of Laser Cutting in Oil & Gas
As laser cutting technology continues to evolve, its impact on the oil and gas industry is likely to grow even further. Advances in automation, precision, and material science will enable manufacturers to create even more sophisticated components that can withstand the extreme conditions of oil and gas operations.
For instance, fiber laser cutting is becoming increasingly popular due to its ability to cut through thicker materials and offer even greater precision than traditional CO2 lasers. This is particularly useful for the oil and gas sector, where components often need to be fabricated from thick, durable metals like steel or titanium.
Moreover, the integration of artificial intelligence (AI) and machine learning into laser cutting systems promises to improve efficiency and accuracy even further. By analyzing data from previous cuts, AI-powered systems can optimize future cuts, reducing material waste and improving overall productivity.
Laser cutting technology has revolutionized the oil and gas industry by offering unprecedented levels of precision, efficiency, and safety. Companies like Rapid Turn Laser & Machine, LLC in Houston, Texas, are at the forefront of this technological shift, providing cutting-edge solutions that meet the demanding needs of the industry.
From pipeline construction to subsea applications, laser cutting is helping to drive innovation, reduce costs, and improve safety in an industry where precision is paramount. As the technology continues to evolve, it will undoubtedly play an even greater role in shaping the future of oil and gas operations, both in Houston and around the world.
By embracing laser cutting, companies in the oil and gas industry can ensure that they remain competitive, efficient, and prepared for the challenges of tomorrow.