Lean manufacturing has become a cornerstone in the evolution of the fabrication industry. By emphasizing efficiency, waste reduction, and continuous improvement, lean manufacturing is transforming how companies operate, compete, and thrive. Rapid Turn Laser & Machine is at the forefront of this transformation, leveraging lean principles to deliver unparalleled quality and service. In this comprehensive blog article, we will explore the fundamentals of lean manufacturing, its significance in the industry, and how it is revolutionizing the fabrication sector.
Understanding Lean Manufacturing
The Origins and Principles of Lean Manufacturing
Lean manufacturing originated from the Toyota Production System (TPS) developed by Taiichi Ohno, Eiji Toyoda, and others in the mid-20th century. The core idea behind lean manufacturing is to create more value for customers with fewer resources by eliminating waste and improving processes. The key principles of lean manufacturing include:
- Value: Define value from the customer’s perspective, ensuring that all activities contribute to what the customer is willing to pay for.
- Value Stream: Identify the entire value stream for each product, mapping all steps and eliminating those that do not add value.
- Flow: Ensure a smooth and uninterrupted flow of products and materials through the production process.
- Pull: Implement a pull system where production is based on actual customer demand, reducing excess inventory.
- Perfection: Strive for continuous improvement (Kaizen) by relentlessly pursuing perfection in all processes.
The Types of Waste in Lean Manufacturing
Lean manufacturing identifies eight types of waste (Muda) that do not add value and should be minimized or eliminated:
- Overproduction: Producing more than what is needed or before it is needed.
- Waiting: Idle time due to delays or bottlenecks.
- Transportation: Unnecessary movement of materials or products.
- Overprocessing: Performing more work or using more resources than necessary.
- Inventory: Excess raw materials, work-in-progress, or finished goods.
- Motion: Unnecessary movement of people or equipment.
- Defects: Producing defective products that require rework or scrapping.
- Non-utilized Talent: Not taking advantage of skills within the organization.
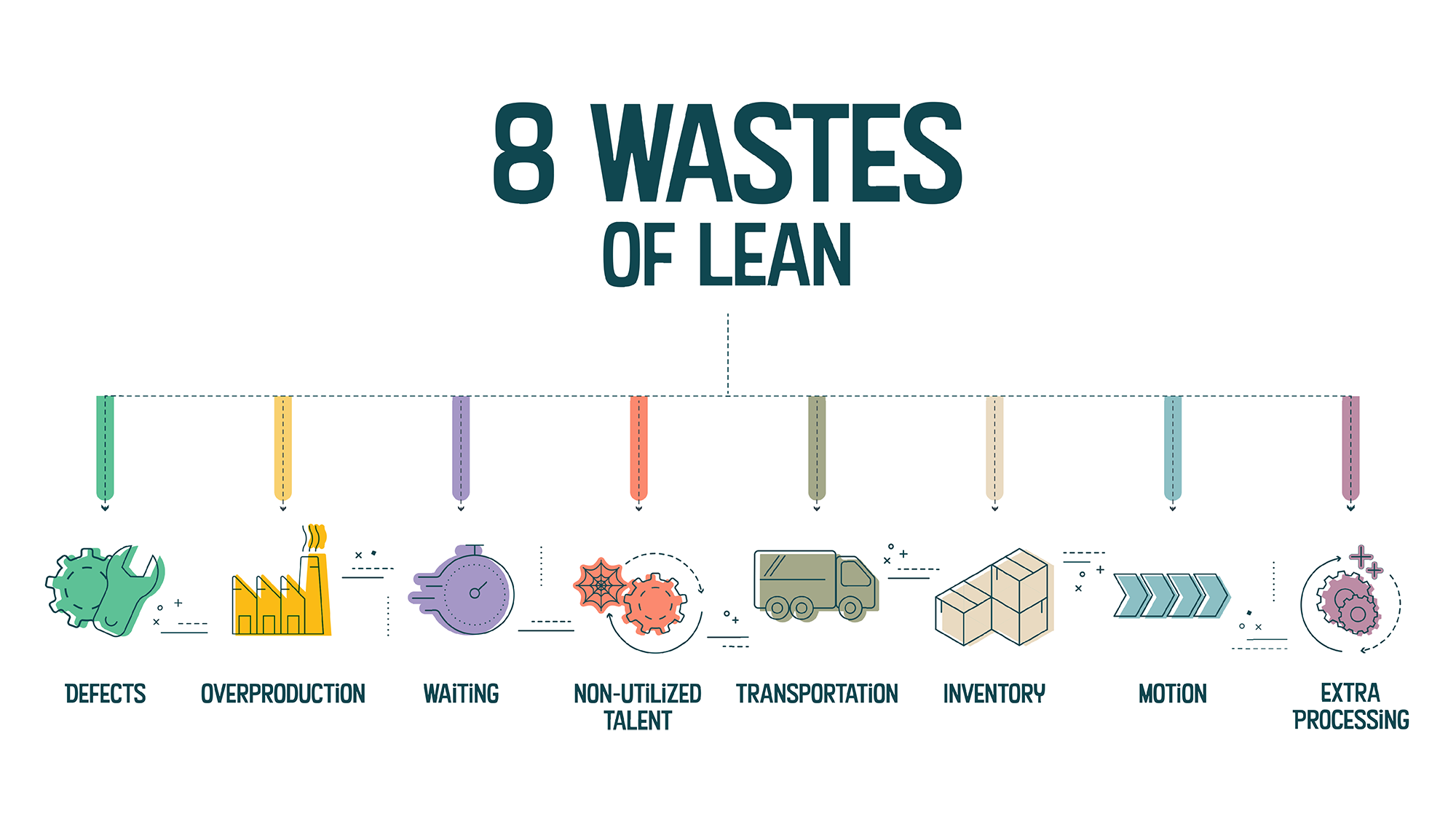
The Importance of Lean Manufacturing in the Fabrication Industry
Enhancing Efficiency and Productivity
Lean manufacturing significantly enhances efficiency and productivity in the fabrication industry. By streamlining processes and eliminating waste, companies can achieve faster production times, reduce costs, and increase output. This is particularly crucial in the highly competitive fabrication sector, where meeting tight deadlines and maintaining cost efficiency are paramount.
Improving Quality and Consistency
Quality is a critical factor in the fabrication industry, where precision and reliability are essential. Lean manufacturing emphasizes continuous improvement and standardized processes, leading to higher quality products with fewer defects. This consistency not only enhances customer satisfaction but also reduces the costs associated with rework and returns.
Reducing Costs and Increasing Profitability
One of the most significant benefits of lean manufacturing is cost reduction. By minimizing waste, optimizing resource use, and improving efficiency, companies can significantly lower their operational costs. This, in turn, leads to higher profitability and a stronger competitive edge in the market.
Fostering Innovation and Flexibility
Lean manufacturing fosters a culture of innovation and flexibility. Continuous improvement encourages employees to identify areas for enhancement and implement innovative solutions. Additionally, the emphasis on flow and pull systems allows companies to respond more quickly to changes in customer demand and market conditions, enhancing their agility and resilience.
Enhancing Employee Engagement and Morale
Involving employees in the continuous improvement process is a fundamental aspect of lean manufacturing. This involvement fosters a sense of ownership and empowerment, leading to higher employee engagement and morale. When employees feel valued and see the impact of their contributions, they are more motivated and productive.
How Lean Manufacturing is Transforming the Fabrication Industry
The Shift to Customer-Centric Production
Lean manufacturing is driving a shift towards customer-centric production in the fabrication industry. By focusing on value from the customer’s perspective and implementing pull systems, companies can better align their production processes with actual customer needs. This alignment reduces lead times, enhances customer satisfaction, and strengthens relationships with clients.
Integration of Advanced Technologies
The integration of advanced technologies is a key aspect of lean manufacturing’s impact on the fabrication industry. Technologies such as automation, robotics, and Industry 4.0 tools enable more precise and efficient production processes. For instance, Rapid Turn Laser & Machine utilizes state-of-the-art laser cutting and machining technologies to enhance precision, speed, and flexibility.
Real-Time Data and Analytics
Lean manufacturing leverages real-time data and analytics to monitor and optimize production processes. By collecting and analyzing data from various stages of production, companies can identify inefficiencies, predict maintenance needs, and make data-driven decisions. This real-time visibility enhances process control, reduces downtime, and improves overall performance.
Sustainable Manufacturing Practices
Sustainability is becoming increasingly important in the fabrication industry, and lean manufacturing plays a crucial role in promoting environmentally friendly practices. By reducing waste, optimizing resource use, and improving energy efficiency, lean manufacturing helps companies minimize their environmental footprint. Sustainable practices not only benefit the environment but also enhance the company’s reputation and compliance with regulations.
Collaboration and Supply Chain Optimization
Lean manufacturing emphasizes collaboration and integration across the supply chain. By fostering strong relationships with suppliers and partners, companies can enhance coordination, reduce lead times, and improve supply chain efficiency. This collaboration is essential for maintaining a smooth and reliable flow of materials and products, especially in a complex and interconnected industry like fabrication.
Rapid Turn Laser & Machine's Lean Transformation
Rapid Turn Laser & Machine has embraced lean manufacturing principles to drive its success and transformation in the fabrication industry. Here are some key initiatives and their impact:
1. Value Stream Mapping and Waste Reduction
Rapid Turn Laser & Machine conducted comprehensive value stream mapping to identify and eliminate waste in its production processes. This initiative led to significant reductions in lead times, inventory levels, and production costs, resulting in more efficient and cost-effective operations.
2. Implementation of 5S Methodology
The company implemented the 5S methodology (Sort, Set in Order, Shine, Standardize, Sustain) to enhance workplace organization and efficiency. This systematic approach improved workflow, reduced clutter, and created a safer and more productive work environment.
3. Adoption of Just-In-Time (JIT) Production
Rapid Turn Laser & Machine adopted Just-In-Time (JIT) production to align production schedules with customer demand. This pull-based system minimized excess inventory, reduced storage costs, and ensured that products were manufactured and delivered precisely when needed.
4. Investment in Advanced Technologies
To further enhance its lean transformation, the company invested in advanced laser cutting and machining technologies. These technologies improved precision, speed, and flexibility, enabling Rapid Turn Laser & Machine to meet diverse customer requirements and maintain a competitive edge.
5. Continuous Improvement and Employee Involvement
Continuous improvement is at the core of Rapid Turn Laser & Machine’s lean strategy. The company fosters a culture of innovation and encourages employees to identify and implement process improvements. Regular training and development programs ensure that employees are equipped with the skills and knowledge to contribute effectively to the lean transformation.
The Future of Lean Manufacturing in the Fabrication Industry
Industry 4.0 and Smart Manufacturing
The future of lean manufacturing in the fabrication industry is closely tied to the advancements in Industry 4.0 and smart manufacturing. Integrating digital technologies such as the Internet of Things (IoT), artificial intelligence (AI), and machine learning can further enhance lean practices by providing real-time insights, predictive analytics, and autonomous decision-making.
Emphasis on Sustainability and Green Manufacturing
Sustainability will continue to be a key focus in the fabrication industry. Lean manufacturing, with its emphasis on waste reduction and resource optimization, aligns well with green manufacturing principles. Companies will increasingly adopt sustainable practices, such as recycling, energy-efficient processes, and sustainable sourcing, to meet regulatory requirements and customer expectations.
Customization and Personalization
As customer demands evolve, the fabrication industry will see a growing emphasis on customization and personalization. Lean manufacturing principles, combined with advanced technologies, will enable companies to offer more tailored products and services while maintaining efficiency and cost-effectiveness.
Collaborative Innovation
Collaboration and innovation will be critical drivers of success in the future of lean manufacturing. Companies will increasingly collaborate with suppliers, partners, and customers to co-create value and develop innovative solutions. This collaborative approach will enhance agility, responsiveness, and competitiveness in the dynamic fabrication industry.
Lean manufacturing is transforming the fabrication industry by enhancing efficiency, improving quality, reducing costs, and fostering innovation. Rapid Turn Laser & Machine exemplifies the successful implementation of lean principles, driving its growth and competitive advantage. As the industry continues to evolve, lean manufacturing will remain a vital strategy for companies seeking to thrive in an increasingly competitive and dynamic market. By embracing lean practices, investing in advanced technologies, and fostering a culture of continuous improvement, fabrication companies can achieve sustainable success and deliver greater value to their customers.